Kimyasal reaktör
Kimyasal reaktörler bir kimyasal reaksiyonun gerçekleştirildiği proses ekipmanlarıdır.[1] Kimya mühendisliğinde proses tasarımı ve analizinde sık kullanılan klasik bir ünite prosesidir. Bir kimyasal reaktörün tasarımı, kimya mühendisliğinin birden fazla unsurunun kullanılmasını gerektirir. Reaktörler proseste ham maddelerin ürünlere dönüştüğü oldukça temel bir ekipman olduğundan proses tasarımı açısından büyük önem arz eder.[2] Kimya mühendisleri bir reaksiyonun net bugünkü değerini en üst düzeye çıkarmak için reaktörler tasarlar. Tasarımcılar satın alma ve işletme maliyetini en düşük seviyelerde tutarken bir yandan da üretilen ürün miktarını en yüksek seviyede tutmak için reaksiyonun ürünler yönünde mümkün olan en yüksek verimle devamlılığını sağlarlar. Enerji girişi, enerji çıkışı, ham madde maliyetleri, işçilik vb. işletme giderlerine örnek olarak verilebilir. Isıtma, soğutma, basıncı artırmak için pompalama, sürtünmeden kaynaklı basınç düşüşü ve çöktürme gibi durumlar da enerji değişimlerine birer örnektir.
Kimya mühendisliği |
---|
Bu başlık kimya mühendisliğine ait serinin bir parçasıdır. |
![]() |
Temel ilkeler |
Ünite prosesleri |
Bakış açıları |
|
Kimyasal reaktörlerin tasarımı ve reaksiyon kinetiğinin incelenmesi, üretim süreçleri için önemli bir konudur. Kimyasal reaksiyon mühendisliği, kimyasal reaktörlerin tasarımı ve özellikle de kimyasal kinetiğin endüstriyel sistemlere uygulanmasıyla ilgilenen bir kimya mühendisliği dalıdır.
Genel bakış
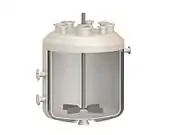
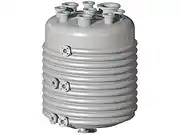
En sık kullanılan temel kimyasal reaktör çeşitleri tank ve boru (laminer akışlı ve piston akışlı reaktörler) tipi reaktörlerdir.
İki çeşit de hem sürekli hem de kesikli reaktör olarak kullanılabilir ve bir veya birden fazla katı madde içerebilir (reaktanlar, katalizörler veya diğer inert maddeler). Ancak reaktanlar ve ürünler büyük çoğunlukla sıvı veya gaz hâldeki akışkanlardır. Sürekli proseslerde reaktörler genellikle yatışkın hâlde çalıştırılırken, kesikli proseslerde geçiş hâlinde çalıştırılmalıdırlar. Bir reaktör ilk kez çalıştırılacağı veya kapatılacağı zaman geçiş halindedir ve ana proses değişkenleri zamanla değişir.[3]
Çeşitli kimyasal reaktörlerin en önemli proses değişkenlerinin tahmin edilebilmesi için kullanılan üç idealleştirilmiş temel model vardır:
- Kesikli reaktör modeli,
- Sürekli karıştırmalı tank reaktör modeli (CSTR),
- Piston akışlı reaktör modeli (PFR).
Pek çok reaktör bu üç temel reaktör çeşidinin farklı tasarımları veya bir arada kullanımı ile modellenebilir.
Ana proses değişkenleri şunlardır:
- Kalma süresi (τ, Yunanca küçük tau harfi)
- Hacim (V)
- Sıcaklık (T)
- Basınç (P)
- Kimyasal maddelerin derişimleri (C1, C2, C3, ... Cn)
- Isı iletim katsayıları (h, U)
Borusal reaktörler (örneğin piston akışlı reaktör) sıklıkla dolgulu yatağa sahiptirler. Bu durumda söz konusu boru veya kanalda katı partiküller veya peletler halinde bir katalizör bulunur.[4] Sıvı veya gaz hâldeki reaktanlar katalizör yatağı boyunca pompalanır.[5] Bu tipe örnek olarak dolgu yataklı reaktörler örnek verilebilir. Bir kimyasal reaktör aynı zamanda akışkan yataklı da olabilir (bkz: Akışkan yataklı reaktör).
Bir reaktörde gerçekleşen kimyasal tepkimeler ısı yayan, yani ekzotermik veya ısı alan, yani endotermik olabilir. Bir tank reaktörün içinde bulunan maddeleri ısıtmak veya soğutmak için reaktörde bir ceket veya reaktör etrafına sarılı borular bulunabilir. Boru tipi reaktörler ise eğer gerçekleşen reaksiyon oldukça ekzotermikse bir ısı değiştirici veya oldukça endotermikse bir endüstriyel fırın gibi tasarlanabilir.[6]
Başlıca reaktör çeşitleri
Reaktörler birçok değişkene göre sınıflandırılabilirler. Reaktörlerin sınıflandırılmasında net ayrımlar bulunmadığından birkaç duruma göre çeşitlere ayrılabilirler.
Çalışma prensibine göre reaktör çeşitleri
Kimyasal reaktörler çalışma prensiplerine göre sınıflandırıldığında üç ana gruba ayrılırlar. Bunlar kesikli, yarı kesikli ve sürekli reaktörlerdir.
Kesikli reaktörler
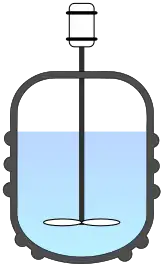
Kesikli reaktörler en temel reaktör çeşididir.[7] Kesikli reaktörler genelde küçük ölçekli üretim faaliyetlerinde ve geliştirilmekte olan yeni proseslerin test edilmesinde kullanılmaktadır. Aynı zamanda pahalı ürünlerin üretiminde ve sürekli operasyona çevrilmesi zor olan proseslerde de kullanılırlar.[8] Pigment, boyar madde, polimer üretimi; süt sanayisi, içecek endüstrisi ve ilaç endüstrisi kesikli reaktörün kullanıldığı alanlardan bazılarıdır.[7][2]
Kesikli reaktörler yatışkın olmayan hâlde çalışırlar. Reaksiyonun gerçekleştiği süre boyunca reaktöre herhangi bir ürün giriş çıkışı yoktur.[8] Ham maddeler (reaktanlar) reaktöre beslenerek reaksiyon başlatılır ve ürünün alınması için belli bir süre beklenir. Sıcaklık ve basıncın kontrol edilmesi, kesikli reaktörler için önemlidir.[7] Gerekli ham maddeler reaktöre tepesinden boşaltılarak istenilen ürün elde edilebilir.[8] Reaksiyon devam ettikçe sıcaklık ve basınçta değişiklik yapılabilir ve yeni maddeler reaktöre eklenebilir.[2]
Kesikli reaktörlerin çeşitli avantajları ve dezavantajları vardır. Reaktanlar kesikli reaktörde uzun süreler boyu bekletilebilir ve bu sayede yüksek ürün dönüşümü elde edilir.[8] Henüz test aşamasında olan ürünlerin üretiminde ve küçük ölçekli faaliyetlerde temizlenmesi ve bakımı kolaydır.[7] Laboratuvar ölçeğinde kullanımında aynı anda birden fazla parametrenin (sıcaklık, basınç vs.) ölçümü kesikli reaktörlerde kolaydır.[9] Ancak reaktörün temizlenmesi ve bakımı için ayrılan süreler üretimi kesintiye uğratır ve büyük ölçekte kullanımında bakımı zordur. Her bir parti ürün için gereken işçilik masrafı fazladır.[7][8]
Yarı kesikli reaktörler
Yarı kesikli reaktörlerin çalışma prensibi hem kesikli hem sürekli reaktörlere benzer. Yarı kesikli bir reaktöre sürekli ham madde beslenirken oluşan ürün sürekli alınmak yerine kesikli bir şekilde alınabilir. Ham madde belli aralıklarla kesikli bir biçimde beslenirken, ürünün sürekli alındığı durum da yarı kesikli bir işlemdir.[2] Yarı kesikli reaktörlerin en önemli kullanım alanlarından birisi, reaksiyonlardaki seçiciliği artırmaktır. Sıvı fazda gerçekleşen birden fazla reaksiyonda istenmeyen ürünler oluşabilir. İstenmeyen ürünün oluşmasının engellenmesi için ham madde beslemesi değiştirilebilir; bir reaktan sürekli beslenirken bir diğer reaktanın da kesikli bir şekilde sisteme beslenmesi sağlanabilir.[8]
Yarı kesikli reaktörler genellikle tank şeklindedir ve görünüm açısından kesikli reaktörler veya sürekli karıştırmalı tank reaktörlere benzerler.[3] Sıcaklık kontrolünün çok iyi sağlanması ve birden fazla sayıda gerçekleşen reaksiyonlarda istenmeyen yan ürünlerin oluşumunun engellenebilmesinden dolayı kullanıma elverişli bir reaktör çeşididir. Ancak büyük ölçekli üretime elverişsiz olması, yüksek işçilik maliyetleri ve reaksiyon analizinin zor olması yarı kesikli reaktörlerin kullanımını sınırlandırmaktadır.[10]
Sürekli reaktörler
Sürekli çalışmakta olan reaktörler neredeyse her zaman yatışkın hâl koşullarında kesinti olmaksızın çalışır. Sürekli ham madde girişi ve ürün çıkışı olduğundan ve sabit operasyon koşullarında (sıcaklık, basınç vs.) tutulduğundan sürekli reaktörler büyük ölçekli endüstriyel üretimlerde kullanıma uygundur.[11] Temel olarak iki tip sürekli reaktör vardır. Bunlar sırasıyla sürekli karıştırmalı tank reaktör ve piston akışlı reaktördür. Dolgu yataklı reaktörler prensip olarak piston akışlı reaktörlerle aynıdırlar, temel fark katalizör bulundurmalarıdır.[8]
Sürekli karıştırmalı tank reaktör (CSTR)
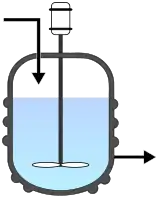
Sürekli karıştırmalı tank reaktörler (continuous stirred tank reactor), sürekli ham madde girişi ve ürün çıkışının olduğu ve reaksiyonun bir tank içerisinde gerçekleştirildiği reaktör çeşididir.[12] Genelde sıvı hâlde gerçekleşen reaksiyonlar için kullanılırlar. Reaksiyonun reaktörün içinde her yerde eşit düzeyde gerçekleşebilmesi için bir karıştırıcıya sahiptirler. Sürekli karıştırmalı tank reaktörler yatışkın hâlde çalıştırıldığından ve karıştırıcıyla "tam" karışımın sağlandığı kabulü yapıldığından, reaksiyon hızının, sıcaklığın ve derişimin zamana ve mekâna bağlı olmadığı kabulleri de yapılarak tasarım eşitlikleri reaktör hacmine bağlı olarak türetilir.[8]
Sürekli karıştırmalı reaktörler endüstrinin pek çok alanında kullanılmaktadırlar. Yağların sabunlaştırılmasında,[3] stiren gibi birçok polimerin üretiminde,[3][13] biyogaz,[14] biyohidrojen[15] ve biyodizel[16] üretiminde, fermantasyonda[17] ve diğer pek çok endüstriyel uygulamada kullanılırlar.
Sürekli karıştırmalı tank reaktörlerin kullanımında belli avantaj ve dezavantajlar vardır.
Avantajları şu şekilde sıralanabilir:
- Sürekli karıştırma sayesinde sıcaklık içerideki sıvıda eşit dağıldığından sıcaklığın kontrolü kolaydır.
- Karıştırmadan dolayı ekzotermik reaksiyonlarda sıvı içinde belli noktalarda aşırı sıcaklık artışı olasılığı düşer.
- Büyük ölçekli üretim faaliyetlerinde ekonomiktir.
- Birbirlerine paralel bağlı kullanıldıklarında düşük mertebeli reaksiyonlar için kullanışlılardır.[3]
Öte yandan dezavantajları da aşağıda sıralandığı gibidir:
- Karıştırma için gerekli enerji, tank reaktörlere ek işletme maliyeti getirir.
- Diğer sürekli çalışan reaktörlere kıyasla reaktörün birim hacmi başına düşen ürün dönüşümü daha azdır.
- İstenen operasyon koşulları için hacimlerinin büyük olması gerekebilir.
- Eğer çıkış akımının boru hattı reaktörde doğru konumlandırılmamışsa ürünün içine reaktan karışabilir.[18][3]
Piston akışlı reaktör (PFR)
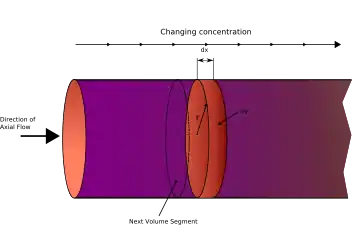
Piston akışlı reaktörler (plug flow reactor) bir boru boyunca sürekli akışın olduğu reaktör çeşididir. Yatışkın hâlde çalışan piston akışlı reaktörlerde reaksiyon silindir boru boyunca gerçekleşmektedir. Piston akışlı reaktöre beslenen reaktanlar reaktör boyunca tüketilerek ürünü oluştururlar. Reaktan ve ürünlerin derişimi, piston akışlı reaktörün uzunluğu boyunca değişim gösterir. Reaktörün başında reaktanların derişimi yüksekken, reaktör çıkışına doğru gidildikçe ürünlerin derişimi yükselir.[8] Bu tip reaktörler genelde gaz tepkimelerinde kullanılırlar ancak bazı durumlarda sıvılarda da kullanılmaktadır.[2]
Piston akışlı reaktörlerin tasarımında da çeşitli kabuller yapılarak tasarım eşitlikleri türetilir. Reaktörün yatışkın hâlde olduğu, derişimin sadece reaktör uzunluğu boyunca ve maddelerin reaktörde kalma süresiyle değiştiği gibi kabuller yapılarak piston akışlı reaktörün uzunluğuna göre tasarım eşitlikleri oluşturulur.[3][8]
Piston akışlı reaktörler sanayide sıklıkla kullanılan reaktör çeşitlerindendir. Benzin üretimi, Haber prosesi ile amonyak üretimi, kükürt dioksitin oksitlenerek kükürt trioksite dönüştürülmesi gibi pek çok üretim sürecinde piston akışlı reaktörler kullanılır.[19]
Herhangi bir karıştırma ekipmanına gerek duyulmaması, büyük ölçekli faaliyetler ve hızlı reaksiyonlar için uygun olması, reaktör hacmi başına yüksek ürün dönüşümü elde edilmesi, piston akışlı reaktörlerin bazı avantajlarındandır. Ancak sıcaklık ve bileşim değişimlerinden dolayı piston akışlı reaktörlerin kontrolü zordur. Ekzotermik reaksiyonlarda reaktörün içinde belli noktalarda aşırı sıcaklık artışı meydana gelebilir.[19][3]
Dolgu yataklı reaktör (PBR)
Dolgu yataklı reaktörlerin (packed bed reactor) çalışma prensibi, piston akışlı reaktörlerle neredeyse aynıdır. Dolgu yataklı reaktörü ayıran fark, reaktörün içinin silindir hat boyu katalizör topaklarıyla dolu olmasıdır. Reaktöre beslenen ham maddeler katalizörlerin arasındaki boşluklardan akarken bir yandan reaksiyona girer ve ürüne dönüşür.[12] Piston akışlı reaktörlerden farklı olarak dolgu yataklı reaktörlerde matematiksel eşitlikler reaktörün uzunluğu yerine katalizör ağırlığına bağlı olarak yazılır ve çözülür.[8]
Dolgu yataklı reaktörler endüstride pek çok yerde kullanılmaktadır. Yüksek sıcaklık ve basınçlarda kullanışlı, katalizörle yüksek temas alanı olduğundan ürün dönüşümü yüksek ve inşa, işletme ve bakım giderleri düşüktür. Ancak tıpkı piston akışlı reaktörler gibi sıcaklığı kontrol altında tutmak zordur. Katalizörlerin yenilenmesi gereklidir. Yan reaksiyonlar oluşabileceği gibi, reaktöre ısı aktarmak da zordur.[20]
Tepkimeye giren maddelerin hâline göre reaktör çeşitleri
Kimyasal reaktörlerde maddenin farklı hâllerinde tepkime gerçekleşebilir. Çalışma prensibine göre bir sınıflandırma yapılabildiği gibi, tepkimeye giren maddelerin fiziksel hâline göre de bir sınıflandırma yapılabilir.
Homojen reaktörler
Homojen reaktörlerde reaktör boyunca tek bir faz bulunur. Yani tepkime denkliğindeki tüm maddeler aynı fiziksel hâlde bulunurlar.[12]
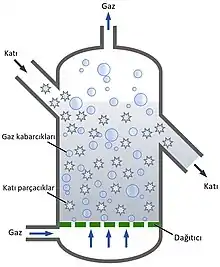
Heterojen reaktörler
Heterojen reaktörlerde birden fazla faz bulunur. Maddeler aynı fazda olsalar bile birbirlerine karışmıyorlarsa heterojen kategorisinde değerlendirilirler. Tepkimeye giren maddelerin hâline göre aşağıdaki gibi sıralanabilirler:
- Sıvı-sıvı hâlinde gerçekleşen reaksiyonlar: Reaksiyonda sadece sıvı maddelerin olması normalde bir homojen reaksiyon olduğu anlamına gelir. Ancak eğer reaksiyona giren sıvılar birbiriyle karışmıyorsa heterojen tepkime gerçekleşir. Reaksiyon karışmayan sıvıların birbiriyle temas ettiği ara yüzeyde gerçekleşir.[12] Ara yüzeyin alanını büyük tutmak amacıyla tank reaktörler kullanılabilir. Benzen veya toluenin asit karışımıyla nitrolanması, emülsiyon polimerizasyonu gibi tepkimeler heterojen reaksiyonlara birer örnektir. Bu tip reaksiyonları içeren kimyasal reaktörler heterojen reaktör tipine başlıca örneklerdendir.[2]
- Sıvı-gaz hâlinde gerçekleşen reaksiyonlar: Heterojen reaktörlerde sıvı ve gaz halindeki maddeler tepkimeye girebilirler. Gaz hâldeki reaktanların reaktöre beslendiği ve sıvının katalizör görevi yaptığı durumlar da mevcuttur. Sıvı ve gaz faz arasında teması artırmak için karıştırmalı tanklar veya boru tipi reaktörler tercih edilebilir.[2]
- Sıvı-katı hâlinde gerçekleşen reaksiyonlar: Sıvı ve katı fazda gerçekleşen reaksiyonlarda her çeşit reaktör geometrisi kullanılabilir. Katı madde bir katalizör veya reaktan olabilir.[2]
- Gaz-katı hâlinde gerçekleşen reaksiyonlar: Kömürün oksijen ile yakılması, gaz ve katı maddeler içeren tepkimelere bir örnektir.[12] Bu tepkimelerde katı madde tepkimede yer alabildiği gibi, katalizör olarak da kullanılabilir.[2] Fabrikalarda kullanılan uçucu organik bileşiklerle kirlenmiş havanın arıtılmasında katı katalizörler kullanılır.[21] Katı katalizör yüzeyine gaz karışımının teması ile gerçekleşen reaksiyonlar bu kategoride değerlendirilir.[22]
- Sıvı-katı-gaz hâlinde gerçekleşen reaksiyonlar: Bu tepkimelerde katı genellikle bir katalizördür. Sıvı ve gaz hâldeki reaktanlar beraber beslenerek reaktörün içindeki katalizör üzerinde tepkimenin gerçekleşmesi sağlanır.[12]
Tepkime türüne göre reaktör çeşitleri
Kimyasal reaktörler gerçekleştirdikleri tepkime çeşidine göre de sınıflandırılabilirler.
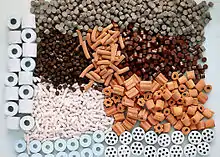
Katalitik reaktörler
Katalizörler bir tepkimenin hızını artıran kimyasal maddelerdir. Günümüzde amonyak üretiminden, hidrokarbonların parçalanmasına kadar pek çok endüstride ve uygulamada katalizörler yaygın olarak kullanılmaktadır. Bu sayede günlük hayatta kullanılan gübre ve yakıt gibi ürünler ve endüstriyel birçok kimyasal üretilebilmektedir. Adından da anlaşılacağı üzere, katalitik reaktörlerde tepkimenin gerçekleşmesine yardımcı bir katalizör bulunur. Bu sayede istenen reaksiyonun hızlı bir şekilde gerçekleşmesi ve kısa sürede çok daha fazla ürün elde edilmesi sağlanır.[22]
Katalitik reaktörlere gaz-katı katalitik reaksiyonların gerçekleştiği reaktörler örnek olarak verilebilir. Gaz-katı katalitik reaksiyonlarda reaksiyonun gerçekleşmesi, reaktanlardan oluşan bir gaz karışımının katı bir katalizör yüzeyine gönderilmesiyle sağlanmaktadır.[22]
Katalitik olmayan reaktörler
Katalitik olmayan reaktörlerde herhangi bir katalizör bulunmaz. Reaksiyon katalizörsüz gerçekleşir. Gaz-katı katalitik olmayan reaksiyonlar bu tepkimelere bir örnektir. Katı atıkların, kömürün vb. organik materyallerin yakılması, demir oksitin yüksek fırınlarda metalik demire indirgenmesi, katalitik olmayan reaksiyonlara birer örnektir.[22]
Galeri
- Değerli metalleri ayrıştırmak için kullanılan deneysel atık işleme ekipmanları.
- Bir karıştırmalı çöktürme tankı.
- Blue Grass Kimyasal Madde İmha Pilot Tesisi'nde bulunan nötralleşme reaktörleri.
- Organik sentez yapan bir sürekli salınımlı reaktör.
- Polonya, Chorula'da bulunan Gorazdze Çimento Fabrikası'ndaki döner fırın.
- Perfloroalkan üretiminde kullanılan kobalt florür bileşiğini üreten bir kimyasal reaktör.
Dış bağlantılar
- LearnChemE tarafından YouTube üzerinde yayınlanmış Kinetik/Reaktör Tasarımı eğitim videoları
- MATLAB ile yapılmış basit CSTR modelleri19 Aralık 2008 tarihinde Wayback Machine sitesinde arşivlendi.
- MATLAB ile CSTR modelleme yöntemi
- Reaktör modellemek için adi diferansiyel denklem (ODE) çözebilen yazılımlar
Kaynakça
- Suresh, S.; Sundaramoorthy, S. (2014-12-18). Green Chemical Engineering: An Introduction to Catalysis, Kinetics, and Chemical Processes. CRC Press. p. 67. ISBN 9781466558854.
- Sinnott, R. K., & Towler, G. (2009). Chemical Engineering Design: SI Edition (5th ed.). Burlington: Elsevier Science. ISBN 9780750685511
- Foutch, G. L., & Johannes, A. H. (2003). Reactors in Process Engineering. Encyclopedia of Physical Science and Technology, 23–43. doi:10.1016/b0-12-227410-5/00654-2
- Jakobsen, Hugo A. (2014-04-02). Chemical Reactor Modeling: Multiphase Reactive Flows. Springer Science+Business Media. p. 1057. ISBN 9783319050928.
- Foley, Alexandra (2014-08-15). "What Is a Packed Bed Reactor?" 20 Ekim 2016 tarihinde Wayback Machine sitesinde arşivlendi.. COMSOL Multiphysics©. from the original on 2016-10-20. Retrieved 2016-10-19.
- Peacock, D. G.; Richardson, J. F. (2012-12-02). Chemical Engineering, Volume 3: Chemical and Biochemical Reactors and Process Control. Elsevier. p. 8. ISBN 0080571549.
- "Visual Encyclopedia of Chemical Engineering: Batch". University of Michigan. 2020. 15 Mart 2013 tarihinde kaynağından arşivlendi. Erişim tarihi: 10 Temmuz 2020.
- Fogler, H. S. (2006). Elements of Chemical Reaction Engineering (İngilizce). Pearson Education Ltd. ISBN 0-13-127839-8. Erişim tarihi: 10 Temmuz 2020.
- Keskin, T., Abubackar, H. N., Arslan, K., & Azbar, N. (2019). Biohydrogen Production From Solid Wastes. Biohydrogen, 321-346. doi:10.1016/b978-0-444-64203-5.00012-5
- "Visual Encyclopedia of Chemical Engineering, Semi-Batch". University of Michigan. 2020. 16 Mart 2013 tarihinde kaynağından arşivlendi. Erişim tarihi: 12 Temmuz 2020.
- Tamaki, M., & Tominaga, H. (1998). 1.4. In Chemical reaction and reactor design (p. 5). New York, NY: Wiley. ISBN 978-0-471-97792-6
- Mann, U. (2017). Reactor Technology. Kirk-Othmer Encyclopedia of Chemical Technology, 1–31. doi:10.1002/0471238961.1805010320011813.a01.pub3
- DeGraff, A. W., & Poehlein, G. W. (1971). Emulsion polymerization of styrene in a single continuous stirred-tank reactor. Journal of Polymer Science Part A-2: Polymer Physics, 9(11), 1955–1976. doi:10.1002/pol.1971.160091103
- Boe, K., & Angelidaki, I. (2009). Serial CSTR digester configuration for improving biogas production from manure. Water Research, 43(1), 166–172. doi:10.1016/j.watres.2008.09.041
- Arooj, M., Han, S., Kim, S., Kim, D., & Shin, H. (2008). Continuous biohydrogen production in a CSTR using starch as a substrate. International Journal of Hydrogen Energy, 33(13), 3289–3294. doi:10.1016/j.ijhydene.2008.04.022
- Chongkhong, S., Tongurai, C., & Chetpattananondh, P. (2009). Continuous esterification for biodiesel production from palm fatty acid distillate using economical process. Renewable Energy, 34(4), 1059–1063. doi:10.1016/j.renene.2008.07.008
- Reungsang, A., Sreela-or, C., & Plangklang, P. (2013). Non-sterile bio-hydrogen fermentation from food waste in a continuous stirred tank reactor (CSTR): Performance and population analysis. International Journal of Hydrogen Energy, 38(35), 15630–15637. doi:10.1016/j.ijhydene.2013.03.138
- "Visual Encyclopedia of Chemical Engineering: CSTR". University of Michigan. 2020. 14 Aralık 2013 tarihinde kaynağından arşivlendi. Erişim tarihi: 10 Temmuz 2020.
- "Visual Encyclopedia of Chemical Engineering: Plug Flow Reactors". University of Michigan. 2020. 12 Aralık 2013 tarihinde kaynağından arşivlendi. Erişim tarihi: 10 Temmuz 2020.
- "Visual Encyclopedia of Chemical Engineering: Packed Bed Reactors". University of Michigan. 2020. 28 Mart 2013 tarihinde kaynağından arşivlendi. Erişim tarihi: 12 Temmuz 2020.
- "Visual Encyclopedia of Chemical Engineering: Catalysts". University of Michigan. 2020. 16 Mart 2013 tarihinde kaynağından arşivlendi. Erişim tarihi: 12 Temmuz 2020.
- Ravi, R., Gummadi, S., & Vinu, R. (2017). Coulson and Richardson's Chemical Engineering: Chemical and Biochemical Reactors and Reaction Engineering. United States, MA: Elsevier. ISBN 978-0-08-101096-9