Birim işlem
Kimya mühendisliğinde ve ilgili alanlarında, ünite operasyonu (veya birim işlem) bir prosesin her bir temel adımına verilen isimdir. Ünite operasyonları ayırma, kristallendirme, buharlaştırma, polimerizasyon, izomerizasyon gibi birçok fiziksel veya kimyasal dönüşümü kapsar. Örneğin sütü işlerken kullanılan homojenizasyon, pastörizasyon ve ambalajlama proseslerinin her biri birer ünite operasyonudur ve hepsi birlikte prosesin bütününü meydana getirirler. Bir proseste, istenilen ürünü başlangıçtaki malzemelerden veya ham maddeden elde etmek için birçok ünite operasyonu gerekebilir. Ünite operasyonları bazı kimyasal değişimleri bünyesinde barındırıyor olsa da, büyük çoğunlukla sadece fiziksel değişimlerin gerçekleştiği durumlar için kullanılan bir ifadedir. Kimyasal dönüşümleri kapsayan süreçlere ise ünite prosesi adı verilir.
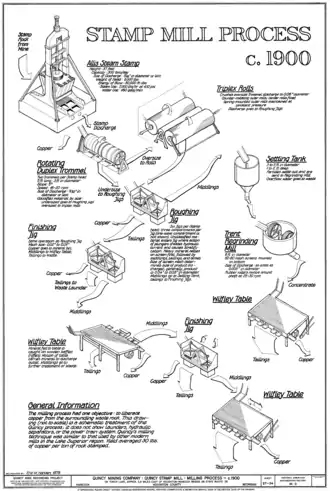
Tarihçe
Tarihte farklı kimya endüstrileri, farklı ilkelere sahip, farklı endüstriyel prosesler olarak görülmüştür. Arthur Dehon Little, 1916'da endüstriyel kimya proseslerini açıklamak için "ünite operasyonları" kavramını öne sürdü.[1] 1923'e gelindiğindeyse, William H. Walker, Warren K. Lewis ve William H. McAdams, "Kimya Mühendisliğinin İlkeleri" adlı kitabı yazdılar ve çeşitli kimya endüstrilerinin aynı fiziksel kanunlara uyan proseslere sahip olduğunu açıkladılar.[2] Bu benzer prosesleri de ünite operasyonu kavramı altında topladılar. Her bir ünite operasyonu aynı fiziksel kanunlara uyar ve ilgili kimya endüstrilerinde kullanılabilir. Örneğin kullanımı, pazarı ve üreticileri birbirinden çok farklı olsa bile bir napalm veya bir yulaf lapasını hazırlamak için kullanılacak olan karıştırıcıyı tasarlamak için aynı mühendislik bilgisi gerekebilir. Ünite operasyonları kimya mühendisliğinin temel ilkelerinden biridir.
Kimya mühendisliğinde ünite operasyonları
Kimya mühendisliği ünite operasyonları beş çeşitten oluşur:
- Akışkan akış prosesleri (akışkanların taşınımı, filtrasyon ve katıların akışkanlaştırılması)
- Isı aktarımı prosesleri (evaporasyon ve ısı değişimi)
- Kütle aktarımı prosesleri (gaz absorpsiyonu, distilasyon, ekstraksiyon, adsorpsiyon ve kurutma)
- Termodinamik prosesler (gaz sıvılaştırma ve soğutma)
- Mekanik prosesler (katıların taşınımı, kırma ve tozlaştırma, ayıklama ve eleme)
Kimya mühendisliği |
---|
Bu başlık kimya mühendisliğine ait serinin bir parçasıdır. |
![]() |
Temel ilkeler |
Ünite prosesleri |
Bakış açıları |
|
Kimya mühendisliği ünite operasyonları aynı zamanda aşağıdaki gibi de sınıflandırılabilir. Aşağıdaki sınıfların her birinde, yukarıda sayılan çeşitlerin bir veya birden fazla unsuru bulunur:
- Birleştirme (karıştırma)
- Ayırma (distilasyon, kristalizasyon)
- Reaksiyon (kimyasal reaksiyon)
Hatta bu kategorileri bile birleştiren reaktif distilasyon, tam karışımlı reaktör gibi ünite işlemleri vardır. Bir ünite operasyonu esasen fiziksel bir taşınım prosesidir ancak karmaşık prosesler için hem fiziksel taşınmanın (örneğin difüzyon) hem de kimyasal reaksiyonun modellenmesi gerekebilir. Bu genelde katalitik reaksiyonların modellenmesinde gerekli olan bir durumdur ve kimyasal reaksiyon mühendisliği adı verilen ayrı bir disiplin altında incelenir.
Kimya mühendisliği ünite operasyonları ve kimya mühendisliği ünite prosesleri, her kimya endüstrisinin temel ilkelerindendir ve kullanılan kimyasal tesislerin, fabrikaların ve ekipmanların tasarımının temelini oluştururlar. Bu iki kavramın bir arada kullanılmasıyla ortaya çıkan üretim süreçlerine kimyasal proses adı verilir.[3]
Ünite operasyonlarının tasarımı, genel olarak her bir temel bileşen için taşınan miktara ait (sonsuz küçük bir miktar da olabilir) dengeleri eşitlikler halinde yazıp, bu eşitlikleri tasarım parametrelerine göre çözdükten sonra ortaya çıkan birkaç çözümden en uygun olanını seçip fiziki ekipmanı tasarlanması ile gerçekleştirilir. Örneğin bir raflı distilasyon kolonunda öncelikle her bir raf için kütle dengesi yazılır. Her raf için bilinmekte olan giriş ve çıkış akımları, sıvı-buhar dengesi ve raf randımanı gibi özellikler toplam kütle akışını verir ve bu yolla kütle dengesi kurulur. Her raf için dengeler birleştirilirse tüm kolona ait bir kütle denkliğine ulaşılır. Bileşen ve enerji dengeleri de kurularak kolonun tasarımı gerçekleştirilmiş olur. Yüksek bir geri akış oranı daha az raf kullanılmasına olanak tanırken, tam tersi durumda daha çok raf kullanmak gerekebilir. Bu sebeple de distilasyon kolonu tasarımında tek bir çözüm yerine bir dizi çözüme ulaşılır. Mühendisler bu aşamadan sonra kolonun kaldırabileceği maksimum hacim miktarı, yüksekliği ve inşaat maliyeti açısından en uygun çözümü bulmak için analiz yapar.
Kaynakça
- "Arther Dehon Little" 11 Mart 2009 tarihinde Wayback Machine sitesinde arşivlendi.. Scatter Acorns That Oaks May Grow. MIT Libraries. Retrieved 13 November 2013.
- "Arthur D. Little, William H. Walker, and Warren K. Lewis" 29 Eylül 2017 tarihinde Wayback Machine sitesinde arşivlendi.. Science History Institute. Retrieved 20 March 2018.
- Shreve, R. N. (1956). The Chemical process industries. New York: McGraw-Hill.